My journey with raku started when I met a young woman (who I have been married to for over 48 years) who was finishing her Master’s degree at Georgia State University. She had to pick up a few hours before graduating and suggested we take a ceramics class together. I was really terrible working with this strange, new material, but was having great fun. I loved working on the potter’s wheel, so decided to continue with a wheel class the following semester. Since I had a bachelor’s degree, I considered a return to college and was able to continue taking independent study classes. Five years later I received my Masters of Visual Arts degree in Ceramics. After graduating in 1980, I decided to become a full-time studio potter rather than trying to find a college teaching position. I had done some raku firing when in school and decided to pursue that type of firing. Now, 44 years later, I’ve done raku exclusively full time and have loved every minute of it! I estimate I’ve done over 12,000 raku firings during that period.
The raku process
Raku is a fast-firing, ceramic process that was first done in Japan over 500 years ago. The Japanese fired their ware in small kilns that were opened when red hot. The pieces were removed and either quenched in water or left to air cool. The Japanese used their raku bowls for the tea ceremony. In 1960 a famous California potter named Paul Soldner ‘Americanized’ the raku process by submerging the quick-fired pottery in combustibles rather than quenching them in water or letting them air cool. Soldner said the glazes were much more interesting using combustibles and so American raku had begun.
I practice the American version. Before the raku firing, the ware must be bisque fired to make the pieces hard enough so they can be glazed. The piece (or pieces) are then fired in my small, hand-built kiln where temperatures are raised to 1850 to 1900°F in about 1 to 1 ½ hours.
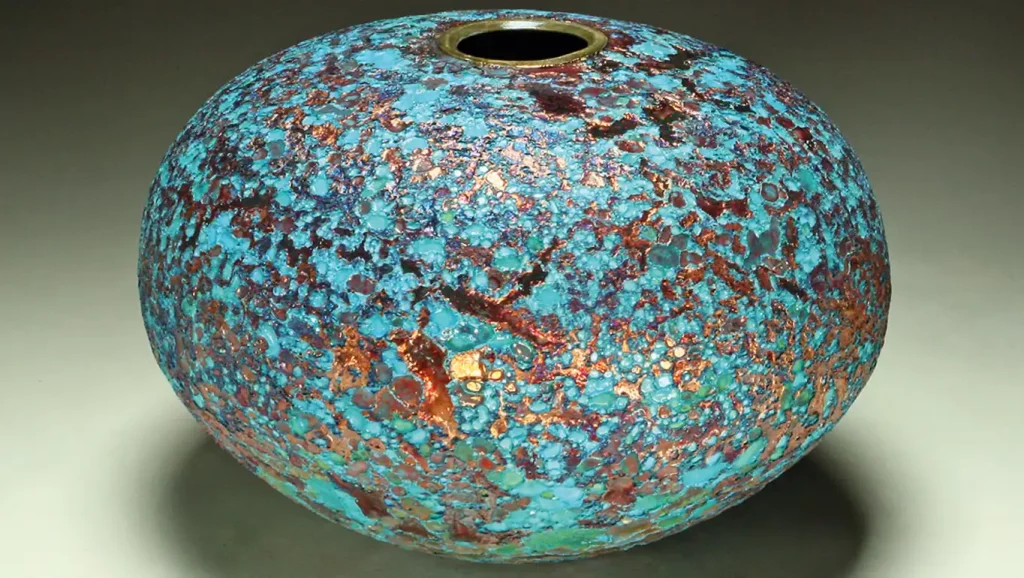
When the desired temperature is reached, I open the kiln by raising the top basket, which allows the hot ware to be easily removed using special tongs. It is then placed in a lidded metal can with combustibles (I use newsprint). Of course, it catches fire immediately and after a few seconds I place the lid on the can, smothering the flames. This creates an oxygen starved atmosphere called reduction, which causes unpredictable changes to the glazes and clay. After about an hour, I open the can and it’s like being a kid at Christmas, as the serendipitous nature of the firing is full of surprises!
The reason I use newsprint is because it gives me more consistency by using the same number and size sheets each time. I use newsprint without print as the ink can sometimes cause unremovable, nasty marks. Other variables that affect the end result are the raku kiln temperature (I generally fire to 1880°F using a pyrometer), the size of the reduction chamber, the amount of time before removing the hot piece from the kiln (I usually wait for about 30 seconds) and the amount of time before the lid is placed on the reduction can (I usually wait about eight seconds). I leave the reduction chamber closed for at least 30 minutes, which gives the ware time to cool slowly. The clay body that I use for raku contains a mineral called kyanite, which counteracts the thermal shock of rapid heating and cooling. Most clays like porcelain and stoneware will often crack when heated and cooled rapidly, so using a clay body formulated specifically for raku is important.
For the last 25 years I have developed all of my glaze recipes, which gives me glazes that are unique and personal. Glazes are made up of mostly insoluble materials that are suspended in water. The materials I choose must be in the proper ratio so the glaze will melt at the desired temperature. A couple of years ago, I discovered a sparkly textured glaze, which is three glazes layered together and then abraded with a hand grinder after the piece cools. I call this my ‘Space Rock’ glaze, as it reminds me of something that might come from outer space. I continue to work on developing and testing new glaze recipes on a regular basis. Many of these are discarded, but when I discover one that is new and beautiful, it makes my heart sing!
Raku is an exciting and spontaneous method of ceramic firing producing one-of-a- kind results. The transformation from a wet lump of clay to the final product is truly alchemistic! Being a raku potter has definitely fulfilled my stated goal of finding something that is stimulating, creative and fun for my life’s work.